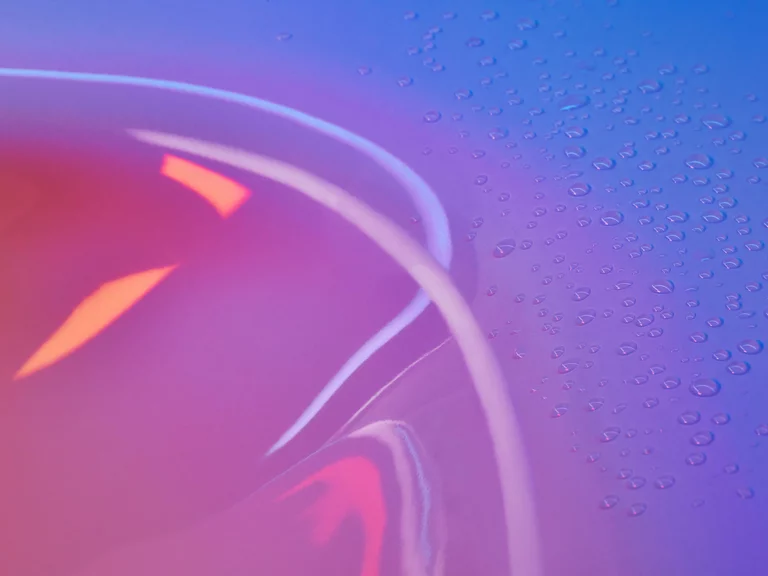
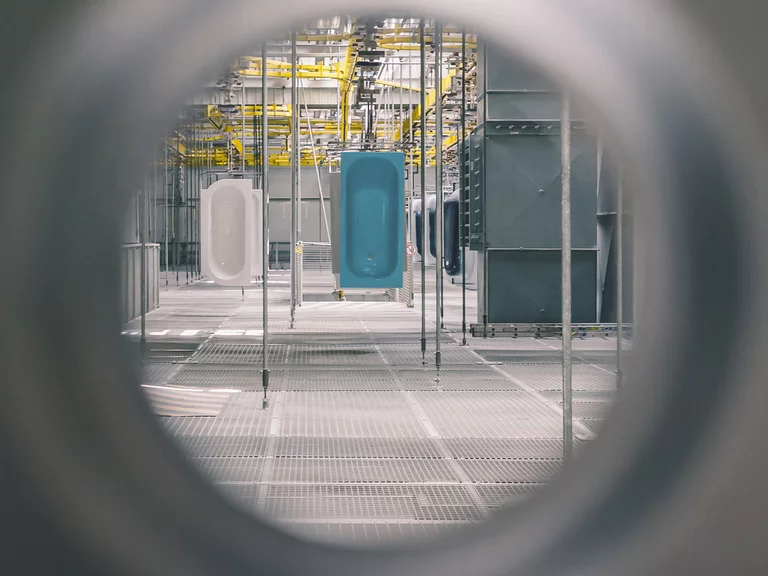
Production
A look behind the scenes
BetteFactory
We believe in quality that lasts. That is why at our production site in Delbrück, we manufacture products for a symbiotic architecture, for the aesthetic and technical unity between a building shell and its interior. With a production capacity of 2,000 items a day, or an annual capacity of around 500,000 components, this is where we produce our high-quality baths, showers and washbasins in glazed titanium steel. Craftsmanship that provides inspiring freedom.
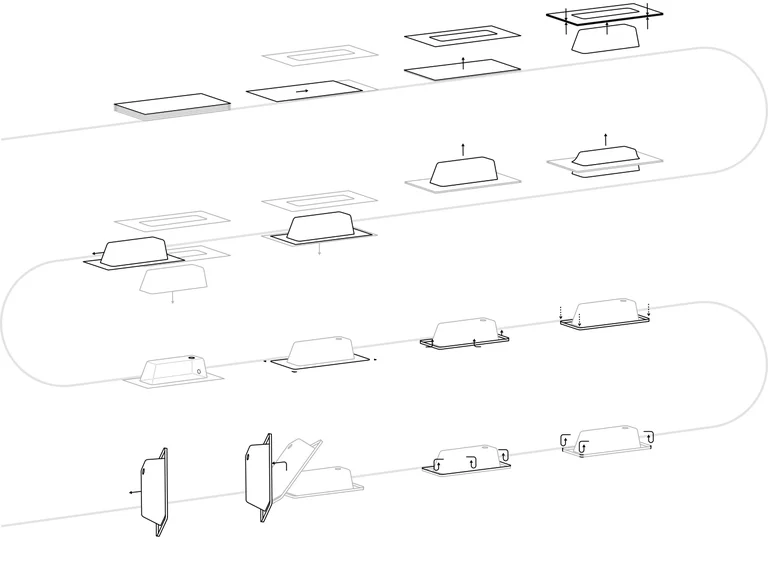
Press line
From the sheet to the blank
We shape dreams out of steel on our press lines. The original press dates back to the 1970s and was designed by Günther Schlichtherle, son-in-law of company founder Heinrich Bette. It was the origin of the entire plant construction and technology in the press shop. Today we have our own tool shop, and we design all our tools ourselves.
Tool store
The basis of perfect bath products
It is the base camp of our production facility and the foundation of perfect bath products: our tool store. Various deep-drawing and edge-machining tools in various shapes and sizes slumber here. All built by yours truly. The weight of a tool: about 5 tons.
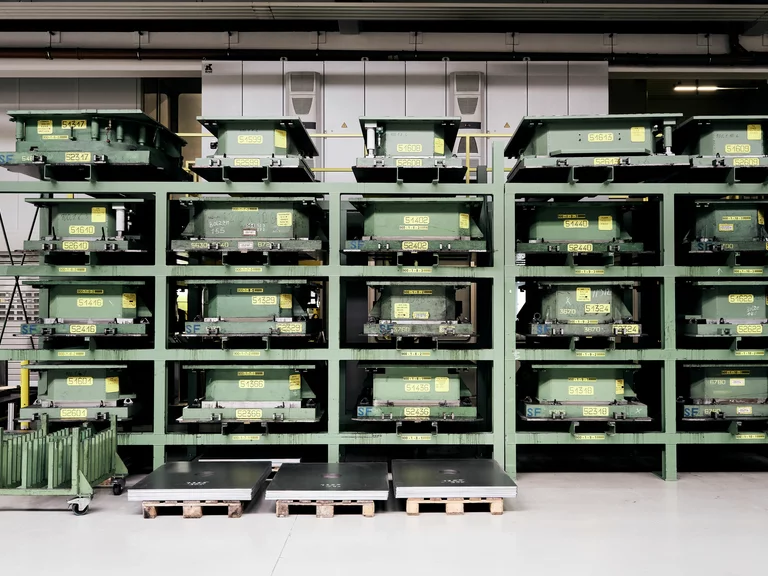
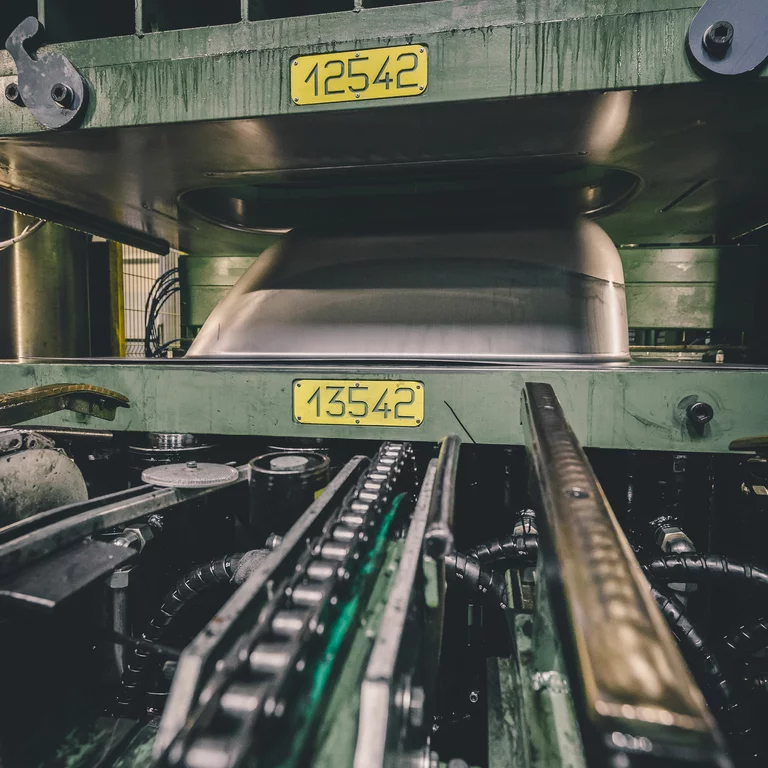
Laser
With millimetre precision
All tools and machines must be set with absolute precision in order to ensure that our products always comply with quality class 1. Such as our laser, which is used on our highly specialised and individual press line 3. It cuts the outer contour of the edges of the bath in such a way that radii and angles can be realised just as precisely further down the line.
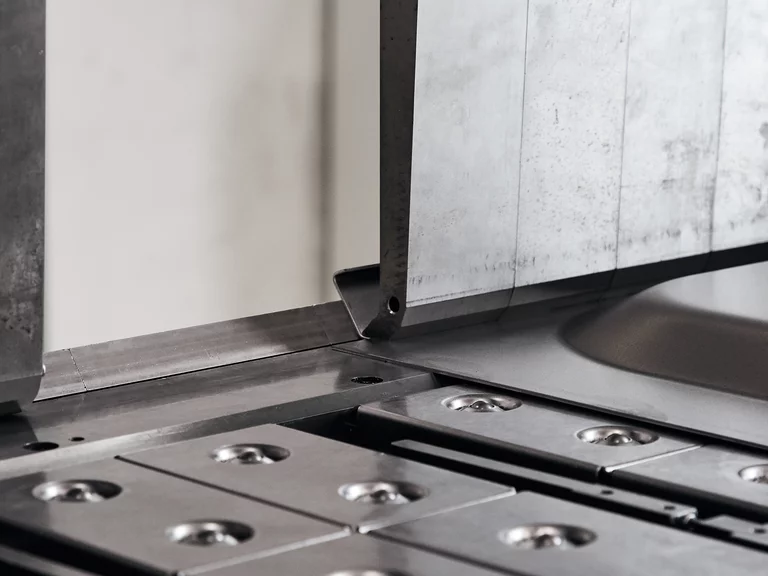
Swivel bending machine
Freedom on a grand scale
We create baths for the future. Both in terms of design and safety – with perfect edges, special size and silicone-free wall connections.
In order to give the rims of our products, for instance, a minimal shape, 250 tons – which is the combined weight of 50 adult elephants – are applied to the material for around 40 seconds. This results in exceptionally narrow rim heights and corner radii.
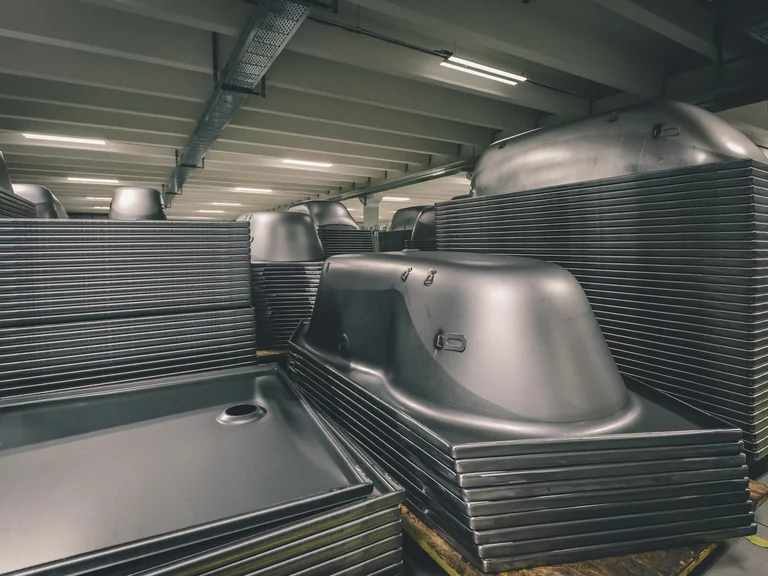
Raw materials warehouse
Reliably available
We always have between 60,000 and 82,000 raw items in our warehouse. From removal, we manufacture 70 percent to order. It only takes about eight hours for the form (raw material) and colour (enamelling) to come together. The products, which are still unprocessed along the edges, are finished individually to the customer's specifications at our manufactory.
Manufacture
Between high-tech and hand-made
Anything that cannot be deep-drawn is shaped and sized by hand in our manufactory. This is where we produce truly unique pieces with master craftsmanship, by carefully finishing many of our models after the automated manufacturing process.
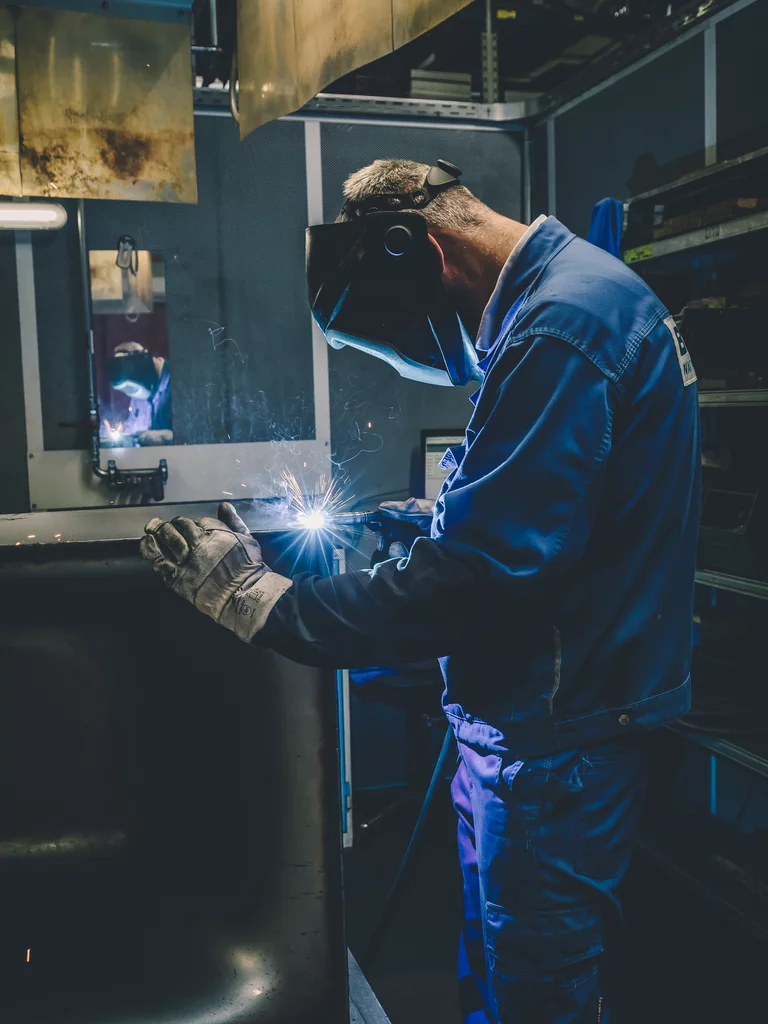
After all, no two bathrooms are the same – and individual needs are for us the measure of all things.
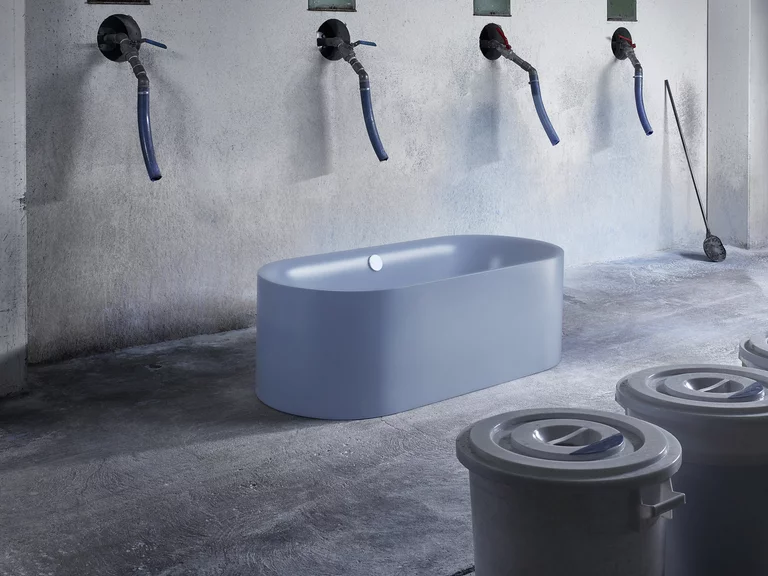
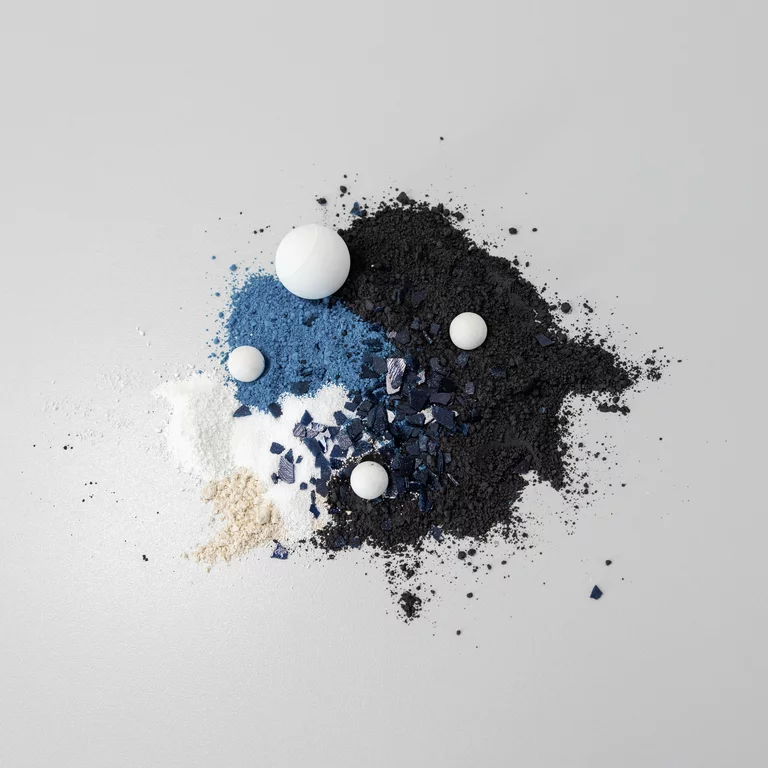
Mill
From raw material to material
Our high-quality enamel emulsion has always been made according to Bette's own recipe.
We obtain the glass splinters for this exclusively from selected specialists.
Known as fries, they are ground in a large mill and then mixed there with other minerals.
At the end, you can choose your favourite from 400 colours.
Enamelling plant
A single unit
Four hand booths - three robot lines - two kilns: In our enamelling plant, our products receive a total of three thin layers of enamel on the inside and one on the back. The thinner, the more flexible and resistant the glaze. Thicker glass panes break quickly - our thin Bette glass fibres remain elastic instead.
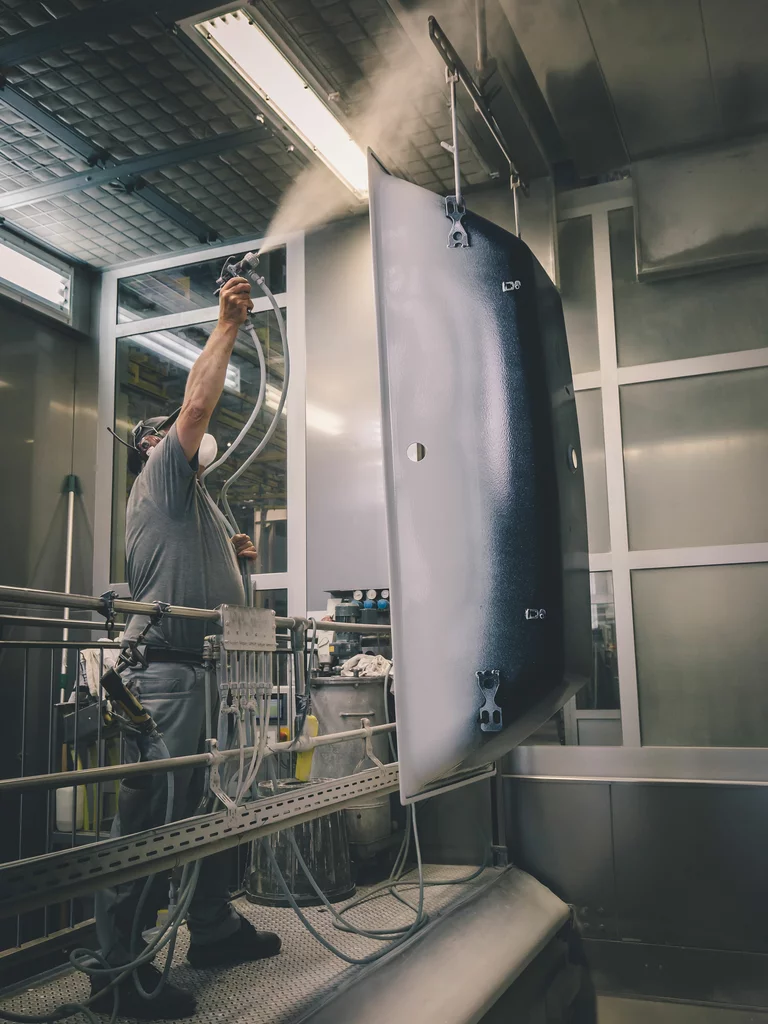
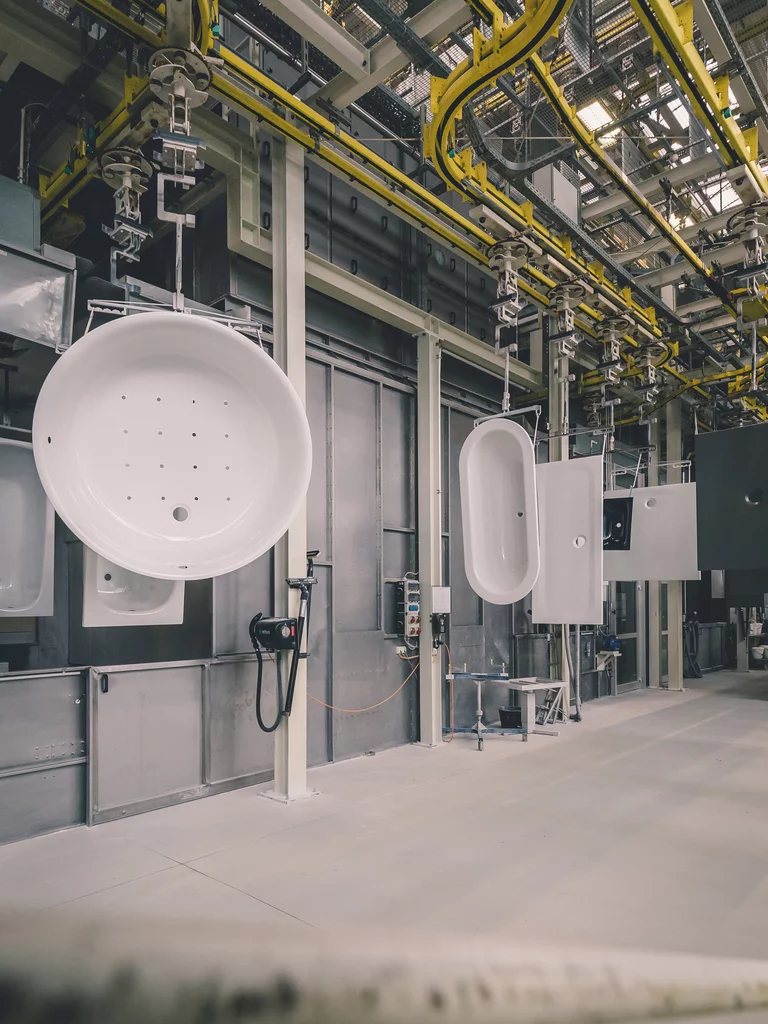
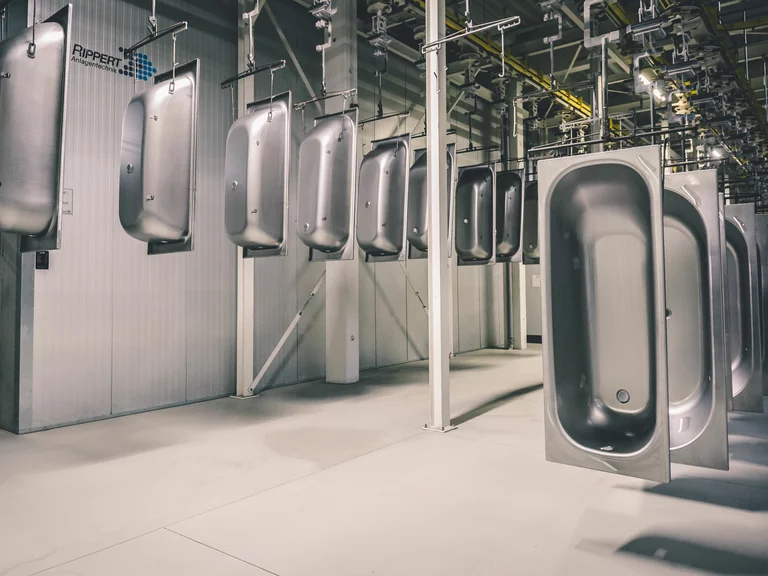
Robot line
Intelligent production assistants
All products that turn white at the end run over the robot line and receive the final layer, our BetteGlaze®, which ensures our brilliant and even surface after the firing process. This is extremely even, uniquely attractive and harder than marble, plastic or steel. Thanks to the precise production control, the robots recognise exactly which geometry they have to spray.
Kiln
Sensory symbiosis
Before our bathroom products go into the kiln, the water is first removed from the wet enamel in the drier. The temperature in the oven is more than 850°C, which melts the enamel so it bonds permanently with the steel in a chemical process. The result is glazed titanium steel with a particularly brilliant and smooth surface that impresses with its absolute robustness.
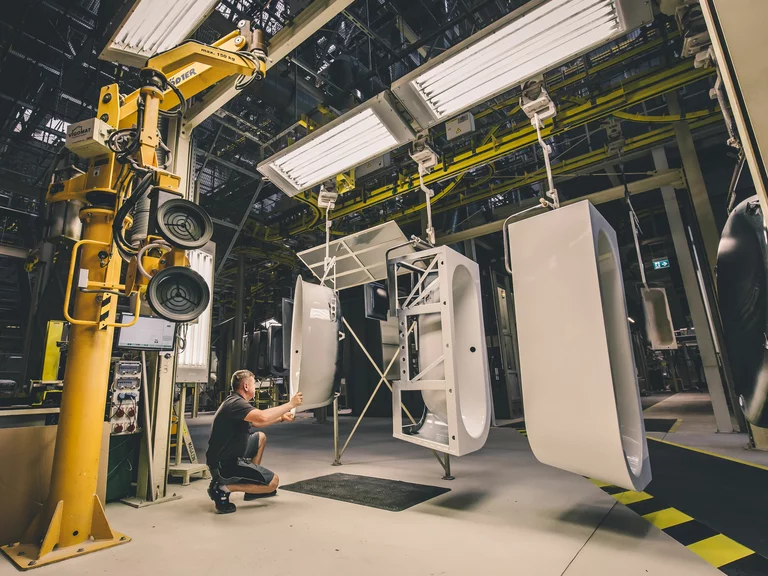
Final check
Precise visual judgement matters here
The final check of each of our products is always visual and carried out by the human eye. This allows even the tiniest abnormalities to be detected so the product can be completely re-enamelled in the event of a visual defect. Our staff work in two to four hour shifts to allow their eyes to rest properly. Only products that have been approved receive the Bette quality seal at the end and are moved by our transport system to the logistics and packaging area.
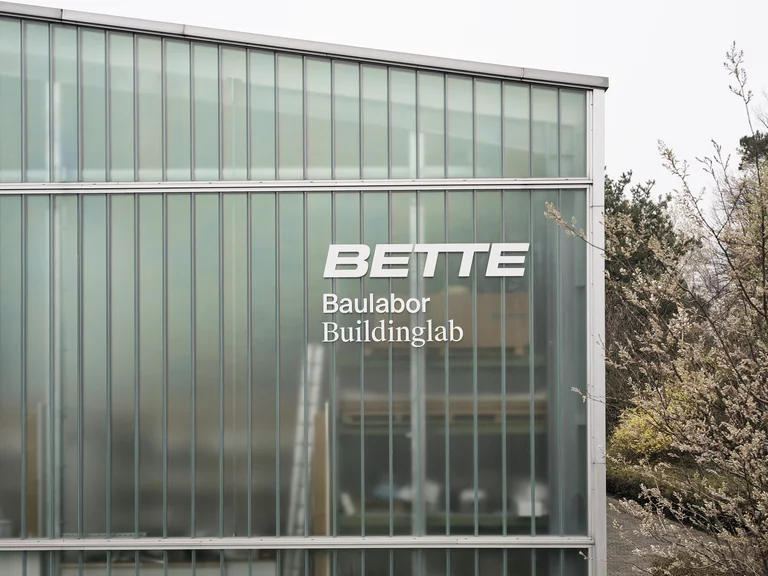
BetteLab
Present meets future
Do it yourself – from assembly to cleaning. The Bette Lab is the authentic interface between the building and the practice-orientated installation technology for Bette products. The heart of the facility is the sound laboratory, in which standard-compliant test cycles relating to sound insulation can be simulated. This house within a house is soundproofed and equipped with highly sensitive measurement technology. Functional and user noises are measured and optimised on real washbasins, baths and shower surfaces. The BetteLab also offers practical space for training courses and lectures for tradesmen, retailers, architects and planners. A real "workbench" for tinkering.
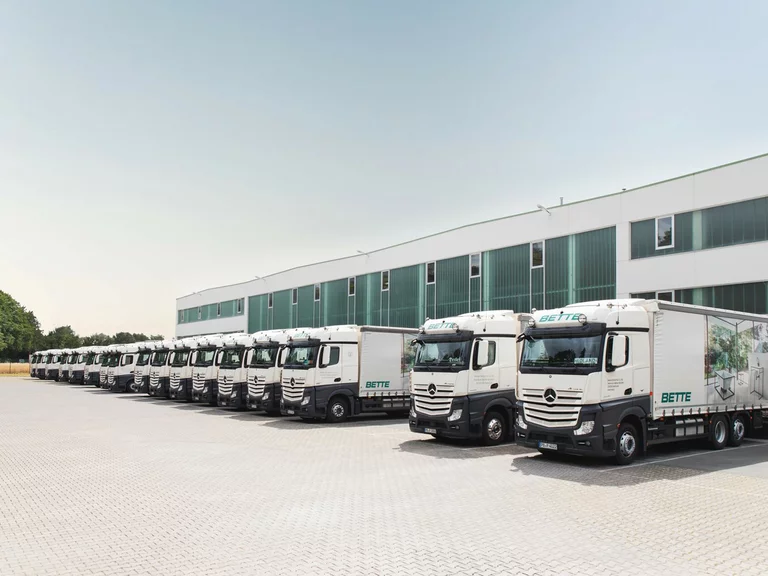
Logistics
Reliability down to the last centimetre
To ensure that our products reach their C9destination safely and on time, we first pick our products according to our customer orders and then pack them according to the highest safety standards. This is followed by the pallet-wise loading of our truck fleet. The most important tool for delivery: the route plan, which specifies the exact unloading sequence. For short and environmentally friendly transport in Central Europe.
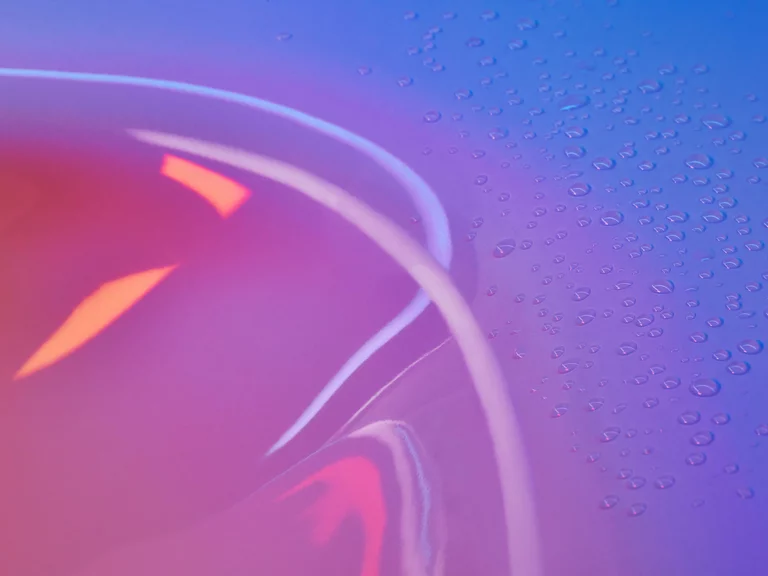
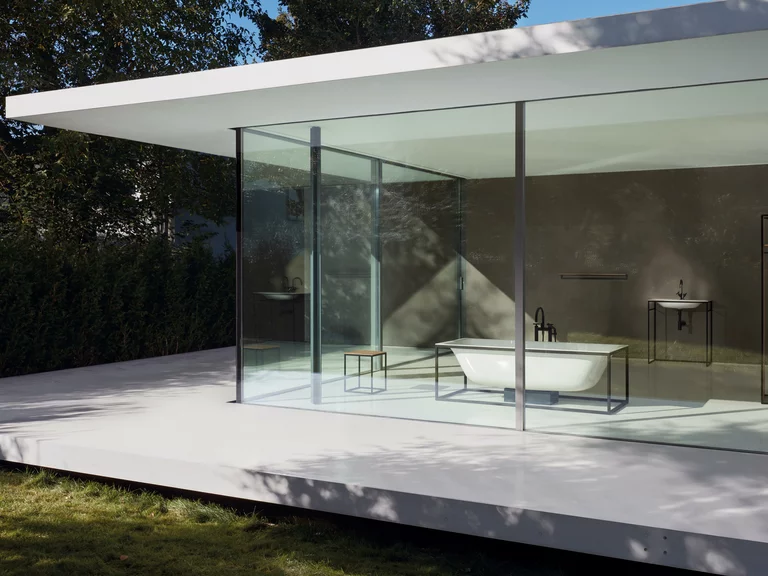